
特集「仕立てへの拘り」#2 金型
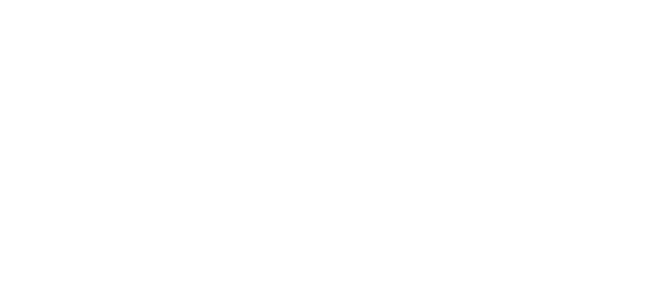
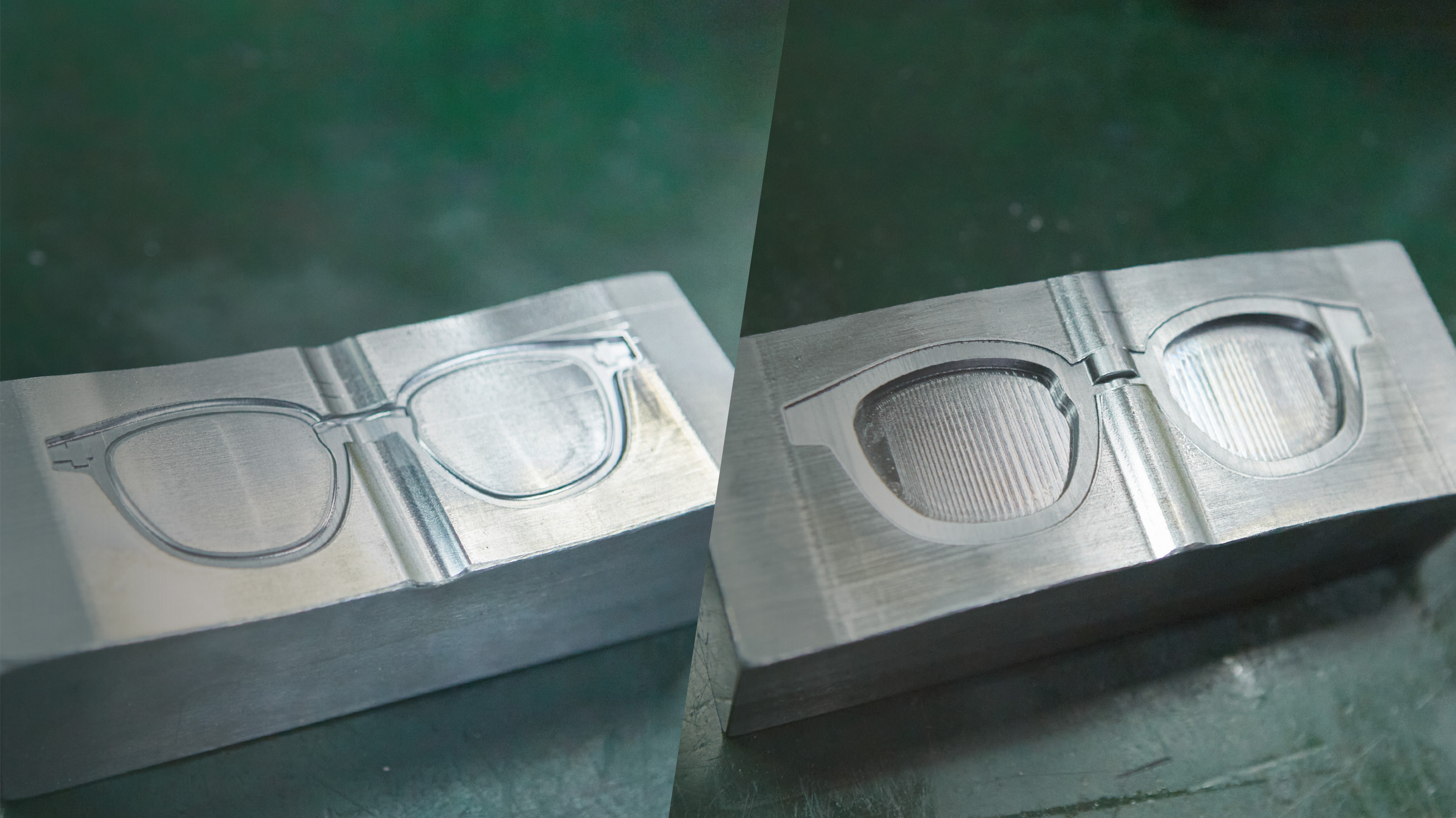
テイラーウィズリスペクトにとって、仕立ての良い眼鏡を造るため欠かせないのが「金型」の質の高さ。
パーツ自体ではないこの部品の重要性を、特集「仕立ての拘り」第2弾としてお届けいたします。
普段ではなかなか耳にすることのできない内容となっておりますので、ぜひお楽しみください。
- 積み重ねから産まれること -
対談
株式会社MAX
中林 まず金型とは、実際のパーツではないので分かりにくいものだけれど、眼鏡の良し悪しをものすごく左右するものと言えばいいかな。
脇 どんなに豪華な家であっても、高性能のエンジンを積んだ車であっても、骨格やベースが悪ければ元も子もないですからね。見た目がいい眼鏡だとしても、道具である眼鏡は、使い続けられる品質があってこそ。そのパーツを生み出すのが金型ですよね。
中林 それとこの金型というものは、一度限りのものではなく、繰り返し使わないといけない。だから最初だけいいものが作れればいい、というものでもないからね。金型は使っていくうちにへたってきてしまうから、そうなるといい部品自体を作れなくなってしまう。そのたびに対応してはコストがかかってしまうし、だからその品質、管理、スケジュール、同じものを何度も作るためにも、同じ品質をいかにできるようにするか。精度と耐久性がものすごく重要になってくる。
そこで体制を整え、今では自社で金型を作れるようになった。当然、多少の費用はかかるんだけれど、この環境のおかげで、常にいい状態の金型を準備して、最良の部品を提供できるようになった。外注していた以前では、コストと時間がかかりすぎていて、この問題が大きかったんだけれども、今では3Dのデータを使い直堀りで金型を調整し、作業が随分と早くなった。
あと正確さにおいても質は上がっているね。コンピュータ制御の切削機CNCマシーン(通称マシニングセンター)の導入と、3Dのデータの活用、そしてこれを管理する能力。スケジュールを共有し、各部署を連動させて全体で動いている。その連動性はうちの強みなのかもしれない。
脇 通常の金型部品屋は、分業制が多いように思うけど、マックスさんは、一貫した体制が整っていて、金型もプレスの工程もお願いすることができます。これは不具合が発生した時にも同じことで、その修正でものすごく助かるんです。
特に新しいデザインを導入したときなんかには、それに対する問題や解決法をご提案してもらえますし、問題を起こさないための話し合いですとか、よきせぬ問題などにも柔軟に対応させてもらえるので、現場の問題解決がスムーズにできます。常に改善策を出しながら進めることができるので、マックスさんにお願いすれば、全てがスムーズに進んでいく。
ものづくりをしていれば予期せぬことはどうしても起こります。当然、工場さんもテイラーのオーダーだけではなく、他社ブランドの注文もありますから、こちらが遅れてしまうことで、予想以上に厳しいスケジュールになってしまう可能性がありますよね。
特に眼鏡業界は分業制になっている業界ですので、外注先が多ければ多いほど遅延する可能性を高めてしまう。だからマックスさんのように一貫した環境を持つ工場さんは、デザイナーにとっては大きな味方です。
脇 できるだけいいものを作りたいという点でも、マックスさんの一貫生産は大きいです。例えば、製造ルートを何本も持っているブランドもあります。そうしたブランドは、納期の問題が起きると、納期を間に合わせるために別の工場に依頼することができる。営業面から考えると、当然そうしたい気持ちはわかります。でもそれをしてしまえば、その製造で得ることができる経験が、あちこちの、そのときそのときで頼んだ工場に分散されてしまいます。商品の質を考えると、そうではなく、できるだけひとつのところにお願いしていきたい。
よりいいものづくりをしたい自分からすれば、常に同じ工場に依頼し、そのときのデザインで起こる、良し悪しを全て理解して進めていくのが理想的です。それはいいバンドが、手の内を理解しているメンバー同士と最高の演奏をするようなもので、昔からやり続けているひとつのチームで動いているからこそ、商品の品質も伴ってくるはずです。一貫体制を持つマックスさんにお願いできることは、理解し合ったひとつのチームのようなものづくりをしたいという、自分にとってもとても理想的なことなんです。
中林 金型の製造も、昔とはだいぶ変わってきて、以前はお客様から言われたものを素直に作ってきたけれど、ここ10年でそうした流れは大きく変わったよね。以前であれば、メーカーから言われたことをそのままやっていた部分が、今は、相手が本当の意味で求めることを、自分たちで考えて、より最適な提案をできるようになった。
それができるようになったのも、色々な機器を導入し、内製化ができるようになったから。このことでさまざまなことが試せるようになり、こちらから提案をできるように変わってきた。コンピューター制御できる機器を導入し、コストと納期を改善し、自分のところでスケジュールをきちんと回す。そうして納期の管理を行えるようになり、コストの削減を考えながらできるようになる。
中林 最近ふと、例えば昔のパーツを見たときに、今だったら別の方法でやってるよ、って自分自身で思うことがある。ただ当時はそれがわからなかったし、そうした模索も今のようにはできなかった。
例えば、テイラーのヨロイのパーツのように、曲げる部分は、以前ならキャストでしていた。当時も脇さんからもキャストは不具合が多いという要望もあったけど、あの頃には今のやり方は思いつかなかったはず。けどそこから新しい技術革新が生まれて、目の前のお題にチャレンジし、解決できる方法を編み出した。そうして新しい技術がどんどん生まれて、それが次の新しい方法となって。
昔は、型を削るマシニングという技術はできなかったから、自分たちが金型を削ることができるという風には考えていなかった。全てがプレスによるもので。だからもし、マシニングをしなくてはならないときには、いつも外注を使わなくてはならなかったけど、マシニングによる二次加工ができるようになったので、できることの幅が一気に広がったよね。
お客さんっていうのは、ちょっとした変更をしてくれっていうことも多い。でもそうしたとき、外注に依頼していると、納期や品質、価格の全てに影響が出てしまう。行き違いも生まれるし、融通も効かなかったりとか、スケジュールが止まってしまうこともあったり。これが内製化できていると、一気に早くなるし、全てコントロールができる。これは分業の多い鯖江が抱える問題の一つでもあるかもしれないけど、うちの場合、ここが一貫しているので、大きなメリットだと言えると思う。
脇 でも、このデザインは無理、ってよくいうじゃないですか?(笑)。
中林 いや俺ができないっていうときは、ほんとにできないときだから(笑)。 例えば、ちょっと前に作ったフレームで、最初は1時間に1枚しかできないっていうのがあったでしょ。でもあれをそのまま進めてしまうと、現実的な商品価格にはならないよね。厳密にできるできないといえば、勿論できるけど、でもそれをできると言っていいのか。1時間1枚でいいのか? この加工だけでこれだと1800円だぞ。ほんとにやるのか? って(笑)。だからそういうことは、やらないって言う。結局はバランスの問題で、部品の加工のひとつで、1800円にもなってしまうようなことがあれば、商品がお客さんに届くときにいくらになるのか? それは果たして妥当か?、となるので、ごめんなさい、これは無理でしょうと(笑)。でもこうした話が、ここだけ(脇と中林さんを指し)の中で決定できるから、話が早いよね。
中林 15年ぐらい前からこういう関係が始まったんだっけ。最初は眼鏡メーカーを通じて依頼してきて。そのころは、言ったことが伝わらない、メーカーはレベルが低い、マックスさんは遅い、なんてよく言われていたけど(笑) 知り合ったころは、俺も確か営業だったけど。
脇 え、そうでしたっけ(笑)。
中林 脇さんとは、年もひとつ差で、お互い関西出身で、おまけに実家も近い。で今住んでる家も近い(笑)。あの黄色のワーゲンに乗っていた頃から知ってるけど、実はめっちゃ近所に住んでいることを知って、今ではヘアカットも奥さんの美容室だから(笑)。
以前はメーカーを飛び越えた関係なんて許されなくて、あいだにメーカーを挟まなければいけなかった。でもそうすることで、話しが伝言ゲームのように変わってしまっていて、大事な情報が、人のあいだを転々とすることで、違うものになってしまう。あの頃は、とにかく縦の関係っていうものが強くて、オーダーを出す側の意見に従うということが強かった。
だから最初の頃は、先にメーカーの担当者に断りを入れて、「直接話させてもらっていいか」っていうところから始まっていたでしょ。そういうところから徐々に関わりが始まって、そのうち、もう全てここで話せばいいよとなり、あらゆることが早くなった。気がつくといつの間にか、決まった内容をメーカーに事後報告する形になり、担当者からも「楽になっていい」って言われるようになって、あの伝言ゲームが終わった(笑)。
脇 ほんとマックスさんがいなかったら、テイラーもここまで来れていただろうかっていうのはよく思うことでして。ここまでいいものを作れるようになったのも、この環境に本当に感謝していますし、マックスさんには、足を向けては寝られないです(笑)。
中林 自分たちもマシニングをするようになって、依頼されたことをただするのではなくて、現場側からも、自分達も眼鏡を作ろうという意識で行うようになった。だから脇さんの高い要望にも答えられるようになったかな(笑)。
脇 でも金型部品製造側として眼鏡についてここまで勉強しようというのも、実は珍しいことなんじゃないかって思うんですよ。でもそこを大切にしてくれるからこそ、製造側から、今の技術でならこうした方がいいのでは? という提案をしてもらえる。
中林 未だに進化している実感もあるしね。確かに工場としては珍しいことなのかも知れないよね。一貫生産に加えて、こうしたところもうちの強みと言えるかな。最初はね、こんなことなんて考えられなかった。マシニング数台ではとても追いつかなかったし。でも、今は30台以上も導入したことで、いろいろな条件が整った。
テイラーのろう付けがないデザインも、今の時代にあっていると思う。いや、いろんなの見ているけど、他のブランドと比べて、玉型とかにも、斬新さも感じるし。時代とマッチしていると思う。今までろう付けするのは地獄だったけれど、パーツをチタン一体で造ることで、ろう付けの加工も減ったしね。外れる、壊れる、っていうのは一体だとないから。
脇 故障する箇所も減りますしね、そうすることで余計な心配も省ける。
中林 全て加工できるマシーンを置いてから変わったよね。それはメリットでしかない。
中林 正直言ってこんなに忙しいことはない。最初は2台から始めたマシニングも、真ん中に1、2台と置いていたけど、今は33台がフル稼働している。忙しいのなら、24時間やれよと言われるけど、そんなことしたら品質が下がる。うちはいいものを造ることを売りにしているし、だからそんなことはしない。もちろん残業もするよ、でも交代制は難しい。そんなことしたら品質管理を誰ができるんだって。
もしかすると、海外の大きな工場との違いは、そこなのかもしれないかなっていうこともある。例え社員が3000人もいたって、品質管理まではできないよ。だからもしかしたら、工場が大きすぎても、眼鏡作りというものはダメなのかもしれないよ。
脇 僕の考えでも同じで、そうなると、いい仕立てができないとなると思っています。
中林 こういう規模でやって、それを理解してもらってっているから、こうしてできている。これが数も増やせ、コストも下げろ、っていう話しだったら、こんな風にはできていないでしょ。他の産業のように、ロボットでやればコストももっと下げれるのかも知れないけど、うちは基本手作業。それは今の質を保つために譲れないところだけれど、この状況から何かを削れと言われても、できることなんて歩留まりを下げれるくらいであって、やってる作業自体はそんなには変えられない。しかも眼鏡は独特だからね。ロボットに任せればいいっていう話ではないと思う。でも、だから鯖江はこんな世の中でも残っているのかも知れないっていうのもあって。やっぱり、せいぜい何万っていうぐらいの製造数がいいものづくりの限度なんじゃないかなっていうのはあるね。
3次元CADを使用し、金型設計するシーン。デザイン図面を元に忠実に再現します(左)。
右画像は、新型の2022AWモデル、カストル。実際に脇がデザインをしているひとコマです。パーツの設計上では、左画像のように、ブロー智のところが開いている設計ですが、仕上がり時のイメージでは、右画像のように、レンズ形状に問題無いよう計算を行っています。目の見えない部分にも手の込んだ技術が隠されているのが、テイラーウィズリスペクトの仕立てです。
3次元CADを使用し、金型設計するシーン。デザイン図面を元に忠実に再現します(上)。
下画像は、新型の2022AWモデル、カストル。実際に脇がデザインをしているひとコマです。パーツの設計上では、上画像のように、ブロー智のところが開いている設計ですが、仕上がり時のイメージでは、下画像のように、レンズ形状に問題無いよう計算を行っています。目の見えない部分にも手の込んだ技術が隠されているのが、テイラーウィズリスペクトの仕立てです。
中林 金型はへたるものだし、使っていくうちにいずれ割れるからお金がかかる。しかもその分もお客さんには請求せず自分持ちにしているし。でも自分のところで造るから原価でできるから。これが外注依頼だったら、きっと費用がもったいないからとなっていくだろうし、そうなると結局商品の質を下げてしまうということになってしまうでしょ。金型が原価でできるからこそ、ダメになったら新しくできるし、惜しみなく使うことができる。そこはほんとに大きいのよ。
この金型の作り方だって、日々色々と工程を変えているし、自分たちの中に、1年でこう、2年後はこう、といった蓄積となる。だから寧ろこの部分は惜しんでいけないところであって、常にステップを踏んで、そこを惜しみなく進化させるからこそ、今に至るわけで。だからとにかくマックスで、ずっとマックスにやってきてっていうそういう自負はある(笑)。
脇 いいものづくりをするためには、ものを造るだけではなくて、それに関わっていただいている方々と、どのように関わっていくのか、これは自分自身としても今後の課題だと感じているのですが、マックスさんにはこれだけのマシーンとスタッフさんがある中で、どうやってこなしているのかも気になります。
中林 今はね、全部署をオンラインでつないで管理してるよ。そうしないと予定なんて決められないって。
脇 え、そうなんですか?
中林 そう、今もマシニングの予定をずっと組んでいて、それに合わせてプレス部品もできてくる。ここも今までの鯖江のやり方とは違うかもしれないんじゃない。だからこのスケジュール管理も、うちのひとつのよさかもな。スケジュールの中で、3次元のデザインからニ次加工まで動かしているのは、うちだけなんじゃないのかなぁ。これはおそらくだけど、マシニングも、鯖江全体でもそんな台がないと思うし、とにかくまだまだ運用しているところは少ないはず。あとはその稼働率だね、そこも大きく違うと思うよ。で、とにかくそれを動かすには段取りが重要だから。
脇 普通、ほんとになかなかできないことではないですよ。技術力、生産能力、そしてスケジュールと。これができている眼鏡工場は少ないと思います。
中林 あと、できるだけいろいろなことを見える化するのも心掛けてますよ。だから当然儲かったことも社員にわかるし、儲かったらもらえるっていうこともわかる(笑)。これはものづくりだけに関したことじゃなくって、常にコミュニケーションをとって、話し合いながらいろんな物事の改善を繰り返しているっていう。ものづくりは、上からこうっていうものではないし、自分だけでできるっていうものではないから。
スタッフにも任せるところは任せることで人も育っていくし、無茶な提案をしてくるお客さんに対しても、こちら側からこうしたらどうですか、という提案も、みんなでできるようになってきた。こういうことが、テイラーの仕立ての良さにも繋がっているってことじゃないない? だからいい眼鏡を造るということは、脇さんと自分だけの関係ではなくて、ここのスタッフも含めて、上も下もなく一緒に作ってるっていう感じのことなんだと思う。人が増えれば当然、意思の疎通も難しくなるのは当然になるし、問題も起きやすい。だから工場を動かす立場としては、そのための段取りとスケジュールを整えていくことが重要で。そして色々な積み重ねの中から生まれることを、次の時代へとしっかり伝えていくことに、自分たちの未来のためにとっても重要になっていくんだよね。
福井県鯖江市を中心とした福井の眼鏡産業は、100年以上もの歴史があり、国内でのシェア率は95%を超えています。今では世界的にも有名な眼鏡の3大産地の一つとして数えられています。この鯖江の成功を支えているのが、世界に先駆けた「チタン」の加工技術です。「チタン」は強度・軽さ・耐熱性・耐食性に優れ、その性質から眼鏡部品には欠かせない素材であり、テイラーウィズリスペクトでは、この産地の高い「チタン」加工技術を活かし、多くの眼鏡デザインを行ってきました。
「チタン」素材を眼鏡に形成していくために、多くの眼鏡工場が採用している技術が、「チタン」に圧力を加える冷間鍛造です。冷間鍛造は精度のバラツキが小さく、複雑・難形状の製品加工も可能な技術。ただし材料(金属)に熱を加えず、常温のまま上下の型により圧力を加える為、加工物の硬度が高く、 大きな成形圧力を必要とします。そのため眼鏡のような、比較的小さいパーツの製造が適しています。材料の利用効率も高いため、コストを抑える効果もあります。
※冷間鍛造は、材料(金属)に熱を加えず 常温のまま圧力を加え鋳造します。一般的に600℃~900℃で行なう鍛造を温間鍛造、それ以上の温度を熱間鍛造と呼ぶ。冷間鍛造は熱間鍛造に比べ精度の高い生産をする事が可能だが、常温の為、加工物の硬度が高く、 大きな成形圧力を必要とする。従って、比較的小さい物の方が適している。
数々の有名アイウェアブランドのデザインを手掛けてきた脇聡が、2017年AWに発表しオリジナルアイウェアブランド。仕立て屋(tailor)という言葉を元に考案したブランド名TAYLOR WITH RESPECTには、制作に関わった全ての人へ敬意が込められている。
持ち主の体に合わせて丁寧に服を仕上げる仕立て屋のような、掛け心地がよくデザイン性の高いメガネ作りがテーマ。オールメイドインジャパンのフレーム